چکیده :
ایجاد سدهای مختلف به منظور کنترل آبهای سطحی افزایش سطح زیر کشت محصولات کشاورزی ایجاد اشتغال وتولید انرژی اراهداف توسعه صنعتی واقتصادی کشور می باشد .انـــرژی پتانسیل انباشته شده ناشی ازارتفاع آب در پشت سددرتوربین آبی تبدیل به انرژی الکتریکی می گردد. یک رانر توربین آبــــــی مدل فرانسیس شامل اجزاء اصلی پره (BLADE) ، تاج (CROWN) ، رینگ پائینی (BAND) تشکیل شده اند که پس از ریخته گری هریک وماشین کاری اولیه به روش جوشکاری به هم اتصال یافته وماشین کاری نهایی می شوند . در فعالیت تحقیقاتی انجام گرفته رانر نیروگاه سد دز مورد مطالعه قرار گرفته ونقشه ها ودانش فنی تولید آن مدون گردید .
مقدمه :
باتوجه به تنوع آب و هوای وعوارض طبیعی وجغرافیایی کشور ایران ایجاد سدهای ابی به منظور تولید انرژی الکتریکی ارزان موجب رشد وشکوفایی کشور درزمینه های صنعتی واقتصادی وجلوگیری ازهدر رفتی مقادیر هنگفتی از منابع آبی وکنترل آب های سطحی وکاهش خسارات ناشی از سیل وفرسایش زمین می گردد. این مهم دربرنامه دوم وسوم توسعه کشور جهت افزایش سطح زیر کشت محصولات کشاورزی ،ایجاد اشتغال وکنترل ابهای سطحی ازاهداف دولت مردان بوده است.استفــاده از توربین های هیدرولیکی به منظور
تولید انرژی از سالهای دور مورد استفاده بشر بوده است
.این نوع توربین ها انرژی پتانسیل ذخیره شده در آب پشت سد را به انرژی مکانیکی تبدیل کرده وسپس درژنراتور انرژی الکتریکی تولید می گردد.(شکل 1)با توجه به منابع های فراوان درایران لزوم انتقال تکنولوژی وتدوین دانش فنی طراحی وساخت توربین های آبی درداخل کشور احساس می گردید که باهمکاری ومساعدت شرکت توانیر موضوع فوق به عنوان یک پروژه تحقیقاتی طرح وتوسعه درشرکت سایا اجراء گردیده است .
روش تحقیق :
یک توربیــن ابی فرانسیـس نویـن از قسمت هـــای اصلی مارپیچ حلزونی , (SPIRAL CASE) رانر (RUNNER) ، رینگ توزیع کننـــده (DISTRIBUTOR) (شکل 2) تشکیل شده است .أیـــن نــوع توربین به نــام مخترع آن جمزبیچنز فرانسیس James Bichens Francis ) )نام گذاری شده است .طی یک صدوپنجاه سال گذشته به تدریج تغییراتی در جهت بهبود و اصلاح Modifica tion) ) توربین های فرانسیس به وجود آمده است . اولین توربین فرانسیس در سال 1847 تـــــولید گردید (شکل 3) سپس در سال 1858 اسوین Swain) (با بهبود پره های توربین فرانسیس جریان مختلط چرخش آب از جهت شعاعی به جهت عمودی در پره های متحرک ابداع نمود در سال 1880 مجرای خروجی آبی به توربین اضافه شده ودرسال 1900 نیز توزیع یک نواخت آب توسط مارپیچ حلزونی (Spiral Case) مورد استفاده قرارگرفت از آن به بعد با پیشرفت در علوم ودانش بشری توربین های فرانسیس نیز متحول شده اند امــروزه از روابط پیچیده ریاضی ومحاسبات کــامپیوتری در طراحی توربین های آبی استفاده می گردد. (شکل 4 الی 8)توربین فرانسیس عکس العملی بوده و با هد متوسط کارمی کند .دراین توربین های نوین فرانسیس جریان در داخل رانر مختلط می باشد . درلبه ورودی پره های متحرک جریان به صورت شعاعی واردشده وازلبه خروجی پره های متحرک جریان به صورت محوری خارج می گردد.به همین دلیل این توربین ها را توربین مختلط نیز می نامند جریان آب پس از عبور رانر به اندازه 90 درجه چرخیده ودریک مجرا با قطر کوچک تخلیه می گردد.لـــوله ورودی آب رااز مخــزن پشت سد به پوسته حلزونی ( Spiral Case ) جهت کاهش مقطع وبه منظور توزیع یکنواخت در تمام نواحی می بـــرد . در داخل رینگ تــوزیع کننده ( Distributor ) یکسری پره های راهنما ( Wicket Gate ) وجـــــود دارند که اب را به اندازه لازم در جهت مناسب به طرف رانـر که در حلقه وسط پره ها قــراردارد هدایت می کننــد . نیرو جنبش آب خارج شده از پره های هـدایت کننده روی پره های رانر باعث نیرو چرخشی رانـر شده که توسط شافت اصلی( Main Shaft ) به ژنراتور منتقل می گردد.اختلاف فشار زیادی بین لبه ورودی ولبه خروجی پره های رانر وجود دارد آب خروجی از رانر فشار کمتر از فشار محیط داشته اما دارای انرژی جنبشی زیادی است برای بازیابی این انرژی یک لوله با شکل جداره واگر ( CONE ) در لبه خروجی رانر به توربین متصل می گردد این لوله اب خروجی از توربین را به عمق زیادی از سطح اب آزاد اطراف توربین می برد . به این ترتیب سرعت آب خارج شده از توربین در خروجی از لوله مکش (Draft Tube ) کاهش یافته وافت انرژی جنبش کم می شود . همچنین فشاردرخروجی پره های رانر پائین آمده ودرنتیجه اختلاف فشار لبه ورودی ولبه خروجی پره های رانر افزایش یافته ودرنهایت موجب افزایش قدرت توربین خواهد شد .همچنین طی تحقیقات انجام شده جدید مشخص شده است که جهت کاهش پدیده کاویتاسیون (Cavition )که عامل تخریب پره رانر می شود لازم است زاویه برخورد آب با پره 15o بیشتر نباشد از طرف دیگر دستاوردهای نوین به منظور یک نواخت نمودن نیرو برپره ها منجر به تغییر شکل پره ها از شکل S به X شده است . (شکل 9)یک رانر فرانسیس از سه جــزء اصلی تحت عنوان پره( (BLADEتاج ( (CROWN، رینگ پائینی (BAND) تشکیل شده است .(شکل 10)پس از طراحی اولیه قطعات به روش ریخته گری از جنس فولاد زنگ زن مارتنزیتی تولید شده وپس از ماشین کاری اولیه شامل خشن تراشی سطوح تاج و رینگ پائینی وماشین کاری نهایی سایر قسمت ها و پره قطعات به روش جوشکاری بهم متصل شده وماشین کـــاری نهایی قطعه رانر انجام می پذیرد قبل از تکمیل ماشین کاری عملیات بالانس کردن رانر انجام شده ودرصورت نیاز در ماشین کاری نهایی تمهیدات لازم در نظر گرفته می شود .
نتایج وبحث :
تهیه نقشه مکانیکی :
با توجه به انتخاب رانر سد دز بعنوان قطعه مناسب جهت نمونه سازی وعدم نقشه های ساخت قطعه فوق الذکر از روش های متداول مترولوژی جهت تهیه نقشه مکانیکی استفاده گردید .سپس به منظور تهیه نقشه پره وموقعیت استقرار پره برروی تاج ورینگ پائینی از روش نمونه برداری توسط مدل نگاتیو کامپوزیتی استفاده گردید .در مرحله بعد مدل پوزیتو پره همراه با قسمت هایی از تاج ورینگ پائینی درون مدل نگاتیو از کامپوزیت شکل گرفت ( شکل 11) به منظور تهیه نقشه دقیق از مدل به دست آمده توسط دستگاه دیجیتال انالایزر CMM نقشه برداری شد . دستگاه دیجیتال CMM از نوع پروب تماسی بوده که توان اسکن احجامی با ابعاد 8 متر طول ، 2 متر عرض و5/2 متر ارتفاع دارا می باشد .داده های به دست آمده از عملیات CMM توسط نرم افزار پیشرفته مهندسی ابتدا به مدل سیمی ( WIREFRAME ) وسپس به مدل توپر (SOLID) تبدیل گردید .ونهایتاً نقشه سه بعدی رانر واجزاء مختلف آن با دقت بسیار بالا تهیه گردید .
بهینه سازی جنس رانر :
در بررسی به عمل آمده جنس رانر اولیه از نوع فولاد کربنی ( CARBON STEEL) باپوشش زنگ نزن معین گردید که پس از مطالعات گسترده با جنس فولاد زنگ نزن مارتنزیتی با مارک GX5CrNiMo13-4 جایگزین گردید .جدول 1 و2 خواص شیمیایی ومکانیکی فولاد مذکوررا نشان می دهد از مزایا استفاده از این نوع فولاد می توان مقاومت بسیار خوب دربرابر خوردگی وپدیده کاویتاسیون وقابلیت ریخته گری وجوشکاری مناسب آن نام برد .
بررسی وتعیین شرایط جریان در ابتدا وانتهای پره متحرک :
در این بررسی از هندسه هیدرولیک سیالات استفاده گردید وموضوعات ذیل مطالعه گردید .شکل گذرگاه رانر
اندازه گذرگاه رانر
تعیین شرایط درورودی وخروجی پره های متحرک
تعیین سرعت نصف النهاری
تعیین مولفه مماسی سرعت در لبه خروجی
تعیین زاویه لبه خروجی پره متحرک
تعیین زاویه لبه ورودی پره
از نتایج به دست آمده تعیین منحنی تاج ومنحنی رینگ پائینی جهت رانر سددز به شرح ذیل می باشد


طراحی وتکنولوژی مدل سازی وریخته گری وعملیات حرارتی :
در طراحی وتکنولوژی مدلسازی قطعات رانر محاسبه مدول قسمت های مختلف قطعه ، انقباض ریخته گری میزان اضافه تراش ماشین کاری سطوخ مختلف سطوح جدایش مدل براساس نوع ماهیچه گذاری سیستم تغذیه گذاری وسیستم راهگاهی وطراحـی جعبه ماهیچه مناسب وسایر ملزومات مــدل انجام می پذیرد .در طراحی وتکنولوژی ریخته گری مراحل تدوین مشخصات ذوب مارک فولاد مصرفی ، درجه حرارت ریخته گری ، نحوه فرمگیری مدل ، نوع مواد مصرفی در قالب و ماهیچه ها ، پوشش سطح قالب وچگونگی خشک کردن قالب ، نحوه نصب مدل وماهیچه ها ومبرد گذاری ومراحل انجام ذوب ریزی واستفاده از مواد حرارت زا(اگزوترمیک) ومواد عایق (ایزوترمیک) انجام می پذیرد .
شبیه سازی کامپیوتری ریخته گری وانجماد :
به منظور بررسی صحت تکنولوژی ریخته گری وبهینه نمودن آن انجام شبیه سازی کــامپیوتری نحوه انجماد ، منحنی های انجماد خطوط ایزوتــرمال سالیدوس ولیکوئیدوس ابــزار مناسبی در تــولید موفقیت آمیز قطعـات پیچیده صنعتی مـــی باشد . در شبیه سازی ابتدا مــدل سه بعدی قطعه تهیه شده وپس از تعیین شرایط مرزی معرفی خواص ذاتی فیزیکی وشیمیایی مذاب ومواد قالب انواع تحلیل های مورد نیاز توسط روش الما نهای محدود (Finite Element Method) انجام می پذیرد (شکل 12 الی 15) سپس نمودارهای عملیات حرارتی شامل عملیات حراتی نرماله کردن وتنش زدایی تدوین می گردد ودستورالعمل جوشکار (WPS) مدون می شود .
مراحل ماشینکاری ، مونتاژ وبالانس رانر:
خشن تراشی سطوح جانبی وفوقانی تاج وماشینکاری نهایی سطوح نحتانی آن
خشن تراشی سطوح جانبی ،خارجی وتحتانی رینگ پائینی وماشینکاری نهایی سطح جانبی داخلی آن
پرداخت سطوح پره وآماده سازی پخ های جوشکاری (Gouging)
نصب پره هادر موقعقت مناسب وجوشکاری پره ها به تاج ورینگ پائینی
انجام عملیات حرارتی تنش زدایی جوشکاری
انجام بالانس استاتیک مجموعه مونتاژی رانر
ماشین کاری نهایی سطوح فوقانی وجانبی رانر
نصب رینگ های جانبی وماشین کاری نهایی آنها
تست وبازرسی مراحل تولید :
-بازرسی مدل ومتعلقات آن
بازرسی های حین فرایند قالبگیری وریخته گری
تعیین آنالیز شیمیایی ودمای مذاب مصرفی
بازرسی های حین عملیات حرارتی
تست های تعیین خواص مکانیک وسختی سنجی
تست های اندازه های ابعادی خشن تراشی
تست های غیر مخرب (NDT) قطعات (UT,MT)
تست جوشکاران PQR
تست های غیر مخرب سطوح جوشکاری شده
برررسی حساسیت قطعه به توازن
تست اندازه های ابعادی نهایی قطعه
بازرسی ونظارت بربسته بندی وحمل
نتیجه گیری :
ساخت وتولید رانرهای فرانسیس مدرن با اندازه ها وابعاد مختلف با امکانات داخلی کشور مقدور بوده واکنون دانش فنی وتکنولوژی لازم در جهت دستیابی به این مهم مهیا می باشد که می تواند در ادامه این فعالیت تحقیقاتی کاربردی اجراء گردد.با توجه به الویت های توسعه صنعتی وعمرانی کشور گسترش نیروگاههای ابی می تواند مهمترین عوامل ایجاد انگیز در سرمایه گذاری درتولید تجهیزات وابسته به این بخش باشد .با توجه به توانمندی وپتانسیل علمی داخل کشور انجام پروژه های تحقیقاتی کاربردی در جهت افزایش راندمان وعمر مفید هسته های مـــرکزی توربین آبی از طریق تحلیل های هیدرولیکی می تواند موجب بهبود عملکرد وبهره وری توربین های آبی کشور گردد.
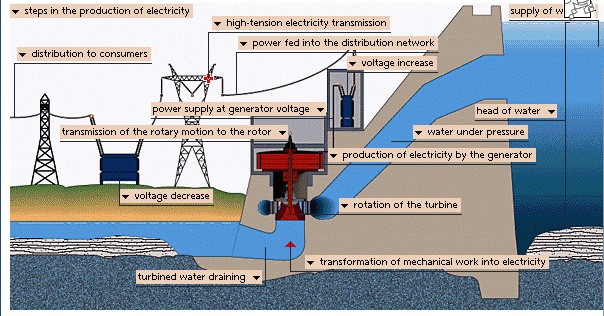
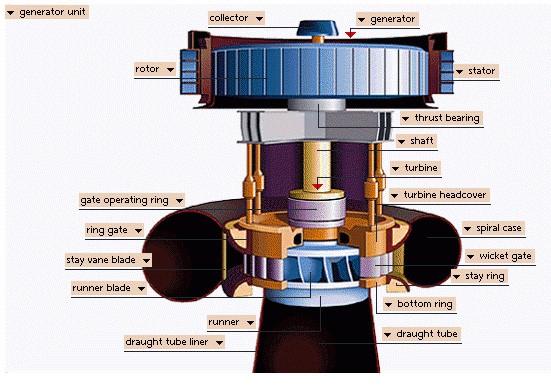
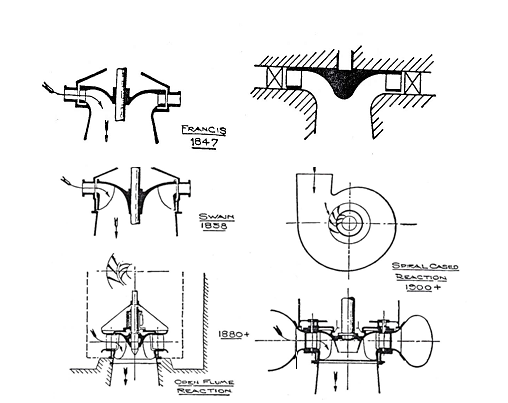
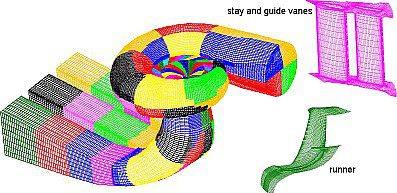
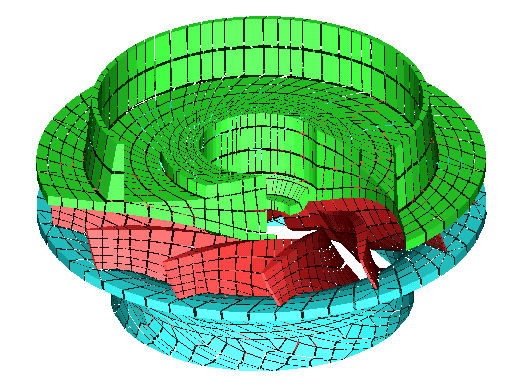
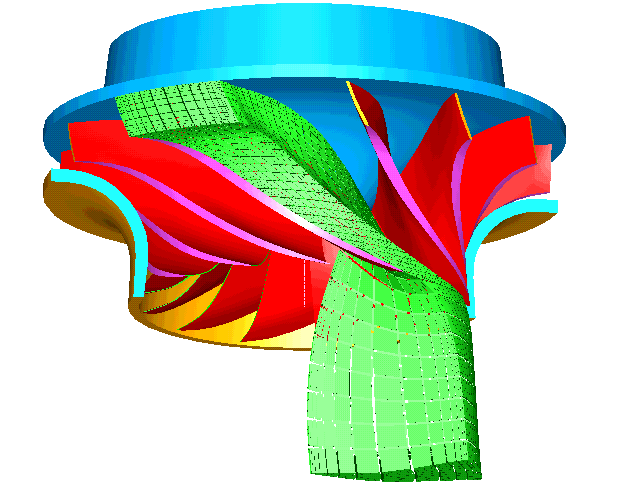
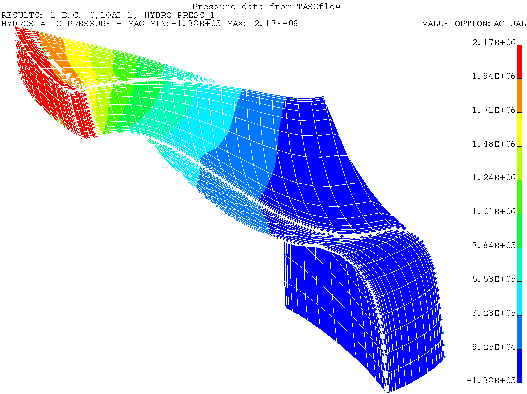
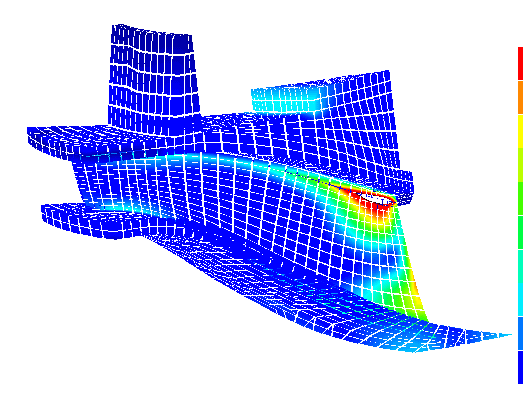
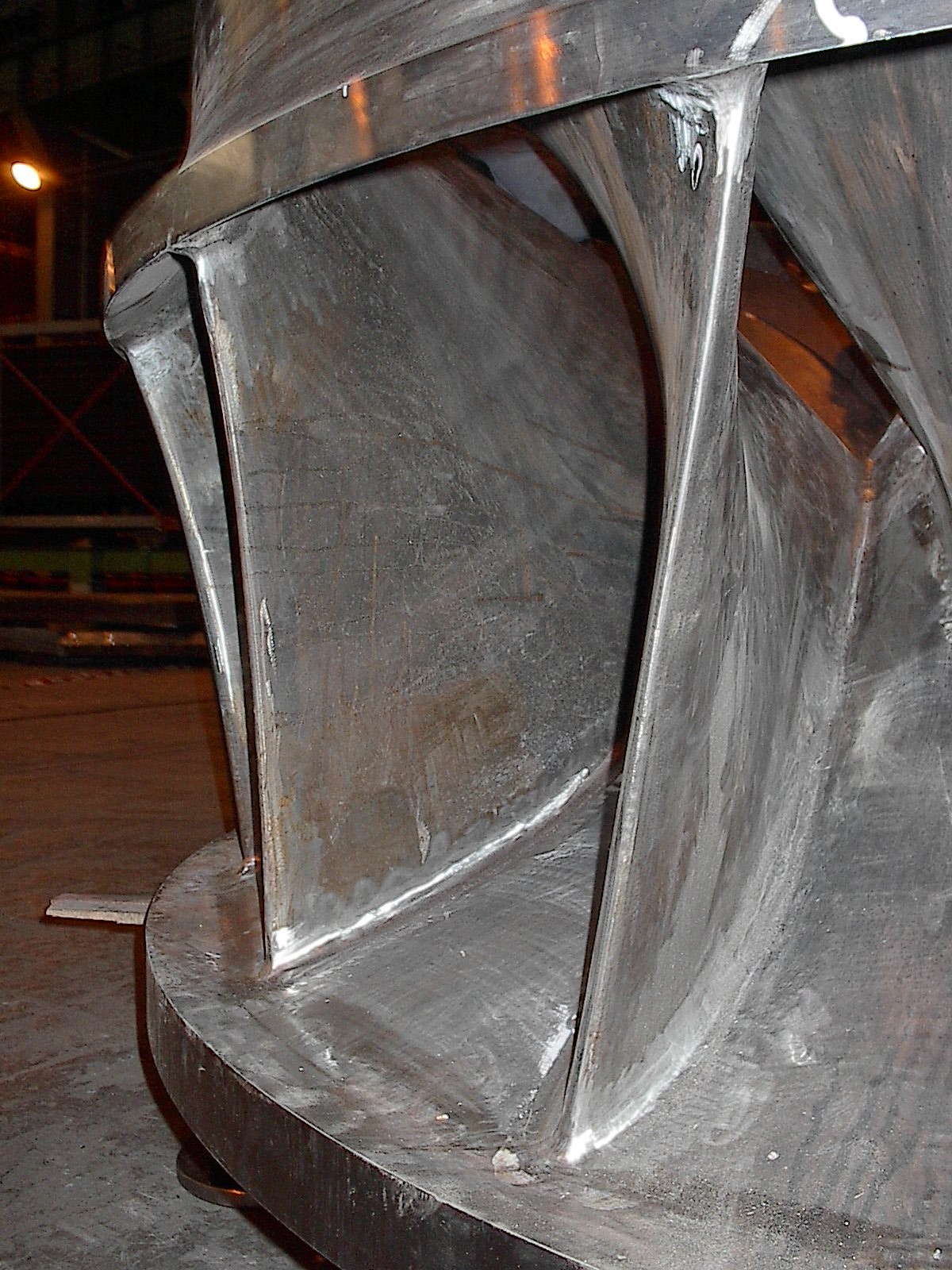
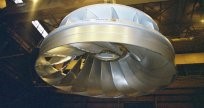
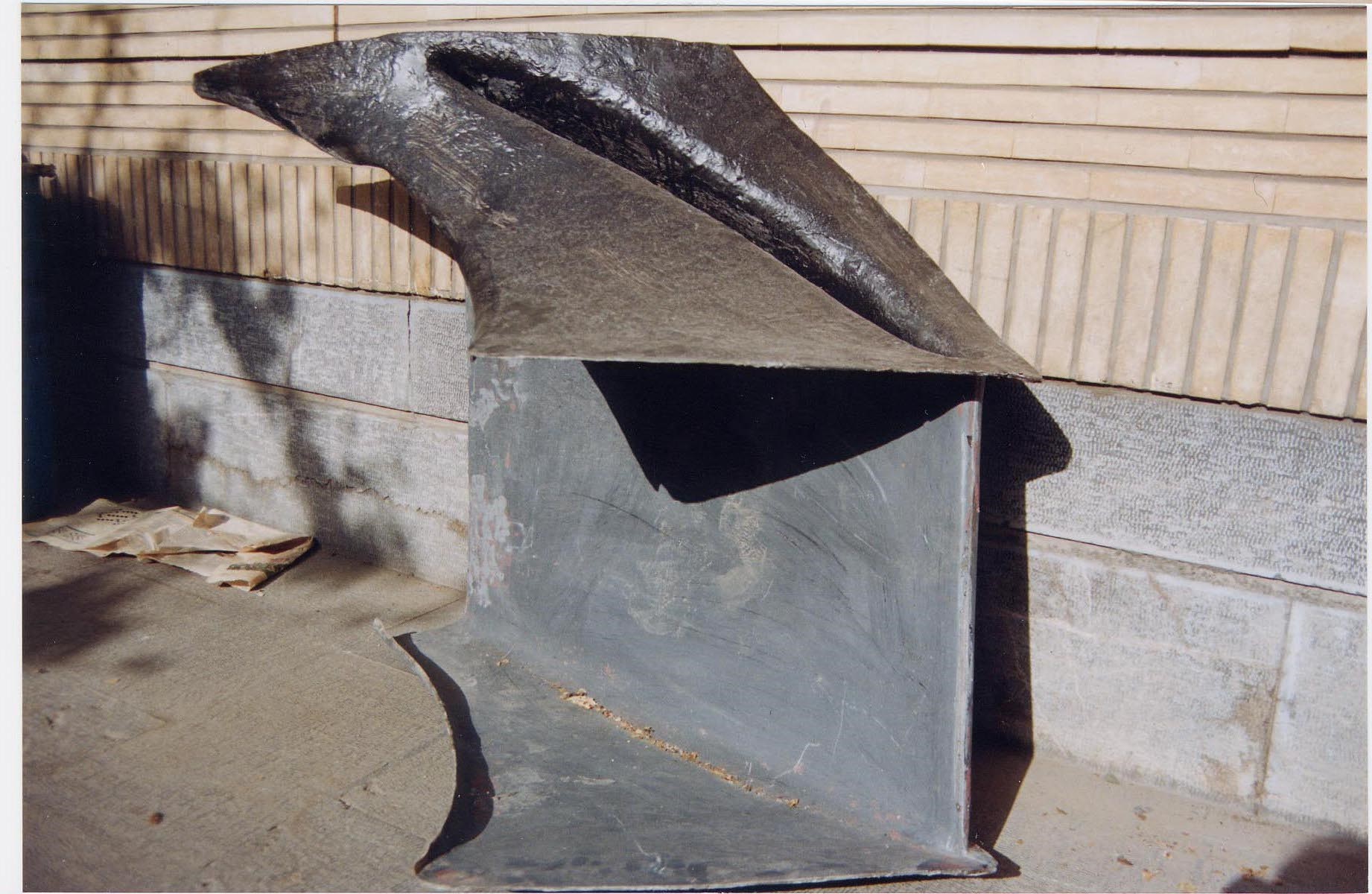
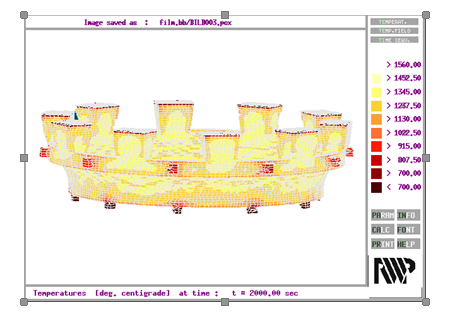
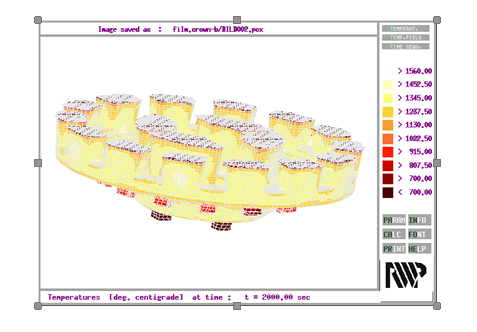
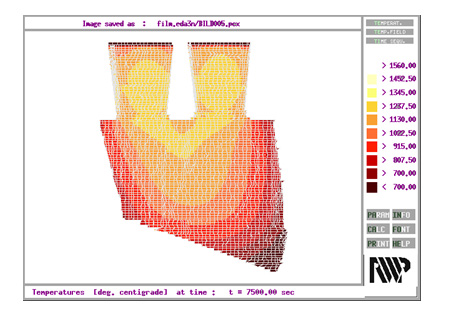
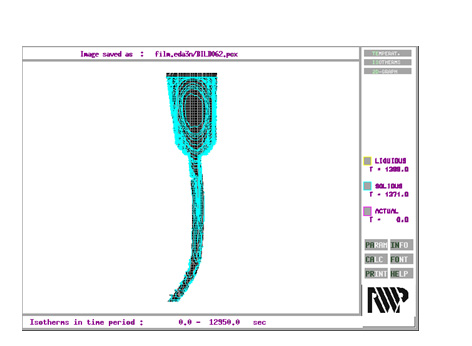
بدون دیدگاه